With the rapid development of the electric vehicle market, the automobile manufacturing industry is facing many challenges and opportunities. Electric vehicle manufacturing requires high-precision and high-quality welding technology to ensure the quality and reliability of parts. It also requires more intelligent production methods to improve production efficiency and reduce costs. In order to meet this demand, Newlas has launched the NewScan-3D Pro remote welding system, which injects powerful intelligent technology into new energy vehicle manufacturing.
Advantages of remote laser welding on the fly
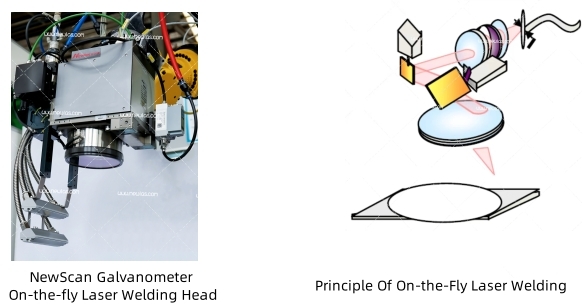
Remote laser welding (RLW) is a non-contact robotic laser welding technology specifically proposed to solve the problem of flying welding during the welding process. Compared with traditional laser welding, remote laser welding can eliminate non-productive moving time. provides higher welding speed, shortens the station cycle time, and provides a variety of welding process modes (circular, straight-shaped, Z-shaped, infinite-shaped, 8-shaped and other special-shaped welding processes).
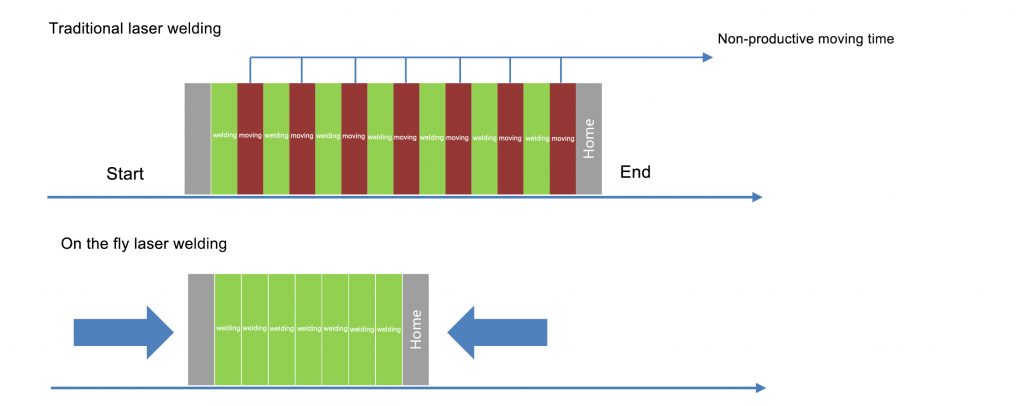
Remote laser welding system
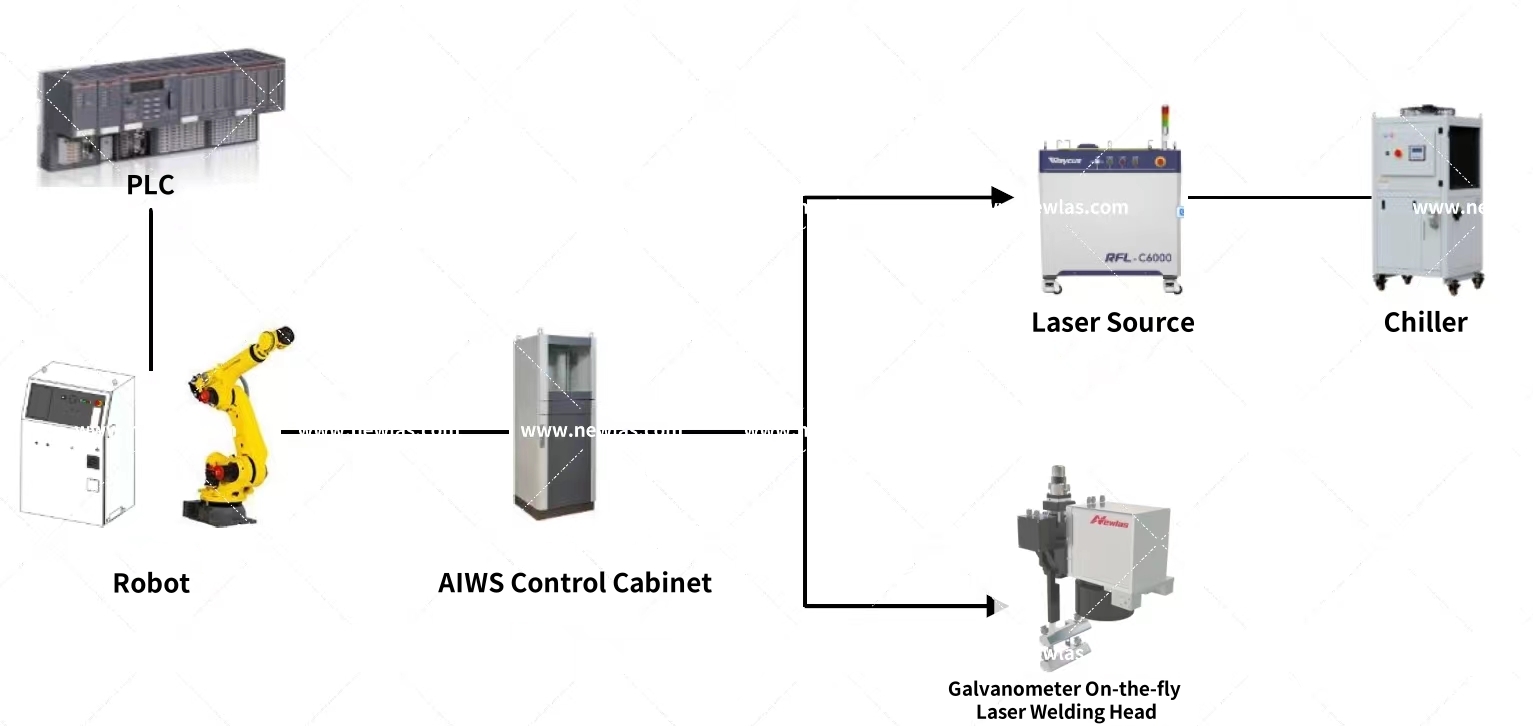
The Newscan 3D Pro remote laser welding system is mainly composed of a robot, AIWS welding process control cabinet, Newscan remote welding head, laser source and chiller. The laser source provides stable laser beam and stable output power. The robot and the remote welding head work synchronously to achieve accurate positioning of the laser welding area, ensuring that the welding system can form various welds while the robot running at a variety of motion speeds.
Advantage
Flying welding: It can be synchronized with the speed of peripheral equipment to realize the flying welding function and improve welding efficiency;
Offline control: Can be separated from the PC and controlled independently, the system operation is more stable and reliable;
Rich interfaces: with bus, I/O, serial port and other various outputs, easy to integrate;
Wide applicability: With its own process database, it can weld different types of materials with different thicknesses, and can be used in many fields such as EV batteries and automobile manufacturing.
Welding process
The Newlas remote laser welding system can customize the welding seam shape, such as circular, straight, Z-shaped, infinite, 8-shaped, etc., to optimize the strength of the welding seam and increase the flexibility of design and process. At the same time, the weld size, weld distribution and weld direction can be customized according to process requirements. The same welding strength can also be achieved on the inside of the workpiece where it is not suitable to reach and the welding cost can be reduced.
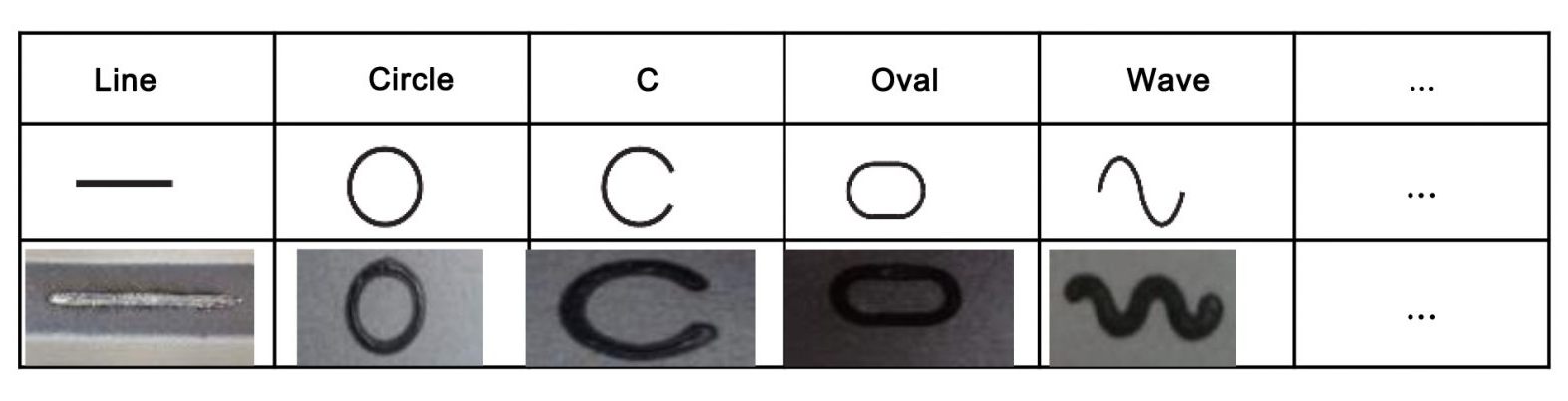
The Newlas remote welding system can record the parameters in the welding process in real time, optimize the welding quality, quickly import 2D CAD graphics, and configure with a human-computer interaction interface.
Application scenarios
Newlas remote welding system can be applied to automobiles and EV battery production lines, such as seats, body-in-white (doors, tail covers, suspensions, side seats and pillars, etc.), interior (rear window sills, hat racks) and motors rotor. In car seats, remote fly welding has been gradually adopted for angle adjusters, frames, guide rails and back panels to improve welding quality and efficiency.
Newlas scanning welding system has been used in SAIC-GM projects and CATL projects.
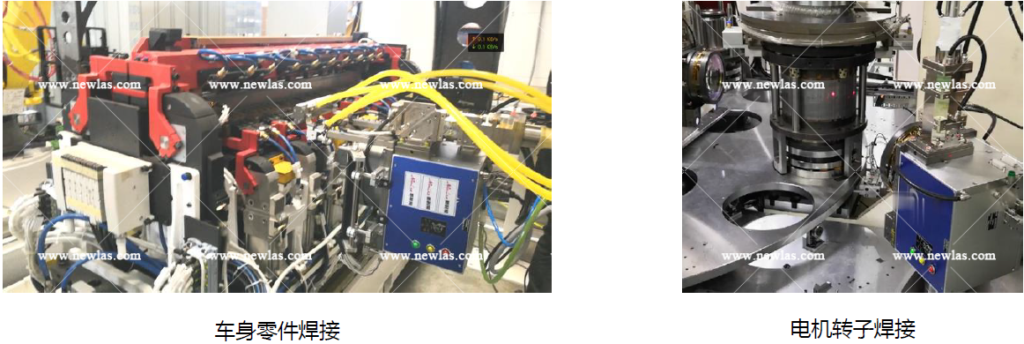
Welding Of Vehicle B0dy Parts Welding Of Electronic Rotary